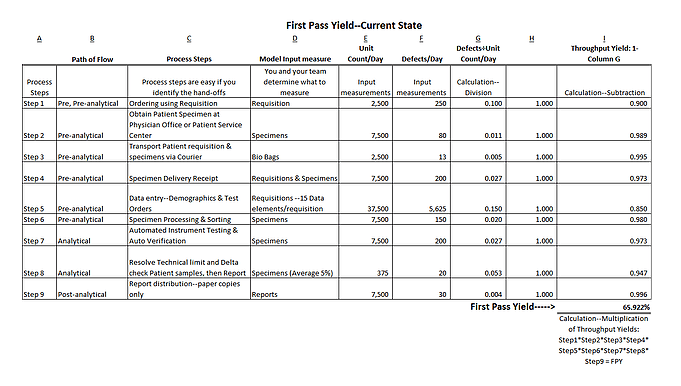
Making sure a PCB design is efficient is a significant challenge. Efficiency in PCB design minimizes waste of expensive materials, and eases the process of making revisions. A highly efficient design means a PCB is more predictable to make; reducing the potential for costly and dangerous errors. Defects can pile up quickly if manufacturers don’t actively monitor production efficiency. A first pass yield in PCB design is a useful metric to describe the efficiency of a design.
What is First Pass Yield in PCB Design?
First pass yield has multiple names, including “quality yield” and “quality rate.” All of these terms mean the same thing: the percentage of completed units in a manufacturing run that meets quality standards. These completed units must be functional upon fabrication; any units that are scrapped or involve any kind of reworking are not included. There are similar metrics for reworked units, such as second pass yield, but they do not measure production efficiency as well as first pass yield.
Manufacturers should measure first pass yield for every unique test state their electronics project goes through. This lowers the probability defects will be missed, and that missed defects will build up over time. For first pass yield to be most reliable—a state called true first pass yield—the metric should take into account two important factors. Firstly, the yield must be unique for every test state and for every project. Secondly, the yield must include all successes and failures—even trivial outcomes. This criterion is particularly important because seemingly trivial failures could be hiding significant defects.
First pass yield can be calculated in a number of different ways, depending on the applications of a PCB project. The common component of the metric is that it measures the cumulative effect of defects on the entire project. Individual first pass yields for pieces of an electronics project could be high, but a single part with a lower yield could dramatically reduce the overall yield for the project. The overall first pass yield of a project could also drop if all the component first class yields are acceptable on their own, but cumulatively result in lower efficiency.
How is First Pass Yield Related to PCB Complexity?
A common way to calculate first pass yield is by relating it to the complexity of a PCB design. Since the first pass yield of an electronics project is a cumulative metric, the more complex the project is, the more difficult it is to achieve a high first pass yield. Many electronics manufacturers use another metric called a complexity index to calculate their yields. This index is a method to numerically represent the complexity of a manufactured product. The number is then related to the successes and failures of a machine run.
There is no universal formula for the complexity index. This is because the complexity of PCB designs can vary widely, and different design elements can have a different impact depending on how current flows through them. There are many different possible equations for the complexity index, and a manufacturer must determine which equation best fits a project’s test data and characteristics. First pass yield calculations can be highly variable due to the complexity index, but the more reliable the complexity index calculation, the more reliable the first pass yield calculation.
A complex PCB project can have a high first pass yield, but it requires extensive testing that can take a lot of time and money. In general, a true first pass yield of 90% or above is acceptable for most electronics projects, although some industries enforce higher numbers. Averages for large industries are usually around 95%, although individual projects may achieve higher yields.
How Should Manufacturers Optimize First Pass Yield?
Optimizing first pass yield isn’t just about getting the number as high as possible. Manufacturers should always remember yield is a metric meant to guide production; it shouldn’t be the ultimate goal of production. For example, it’s almost impossible to achieve a perfect first pass yield because every machine run is bound to have an occasional defect or bad batch. If a manufacturer’s goal is to achieve a 100% first pass yield, they’ll never move past testing. It’s important to make a PCB design as efficient as possible, but every design reaches a point where the pursuit of perfection begins to lower efficiency. Finding the balance between these concerns is the best strategy to optimize first pass yield.
It’s also important to be sure a first pass yield calculation takes enough information into account. A high first pass yield is not necessarily an accurate measure of the efficiency of an electronic project. Manufacturers should test as many project components, configurations, and usage scenarios as possible. The more component first pass yields become available from this testing, the more accurate the cumulative first pass yield metric will be. Testing five areas of an electronics project and getting a perfect yield is less reliable than testing twenty-five areas and obtaining a lower yield.
First pass yield optimization is important because it provides evaluations of where manufacturing can improve, and how those improvements can be made quickly. Using yield percentages as a guide can make manufacturing easier, and provide the basis for future innovations.
Ultra Librarian provides reliable components for PCB designers that keep the first pass yield in PCB designs high. Working with Ultra Librarian takes the guesswork out of preparing for your next great device and puts your ideas on the road to success. Register today for free!