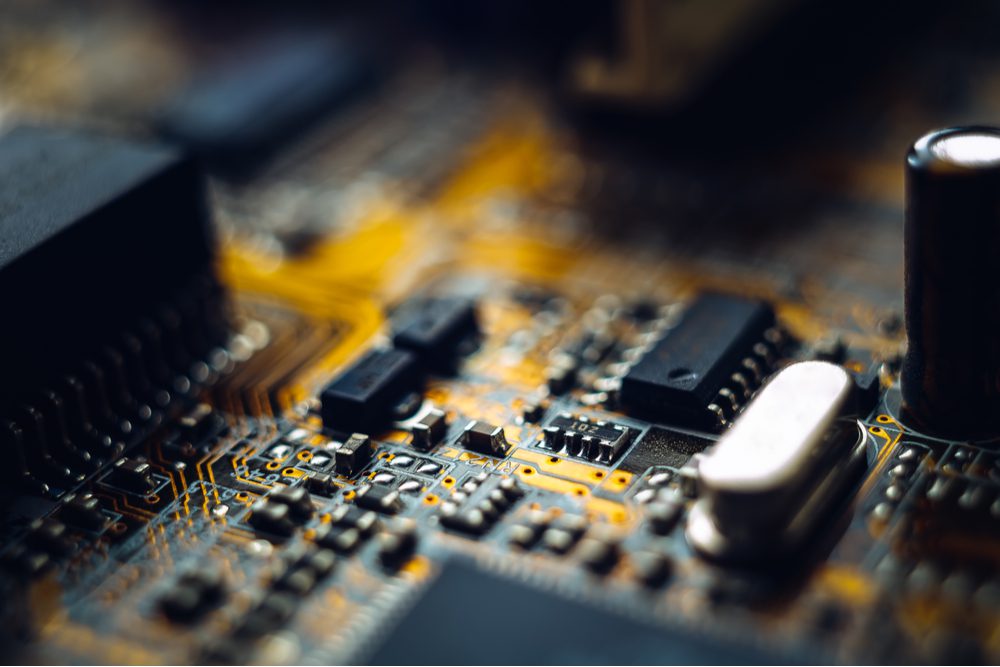
When building a new electronics project, many designers strive to use the most updated components available. However, technology advances every year, so even the most advanced components inevitably become obsolete. It is important for engineers to create projects to maximize the lifetime of their end products, keeping in mind that component lifespan can vary as well.
Designers should view obsolete electronic components not as a failure on their part, but as an opportunity to remake their designs into something better. Individual designers and large electronics companies can all benefit from identifying and removing obsolete components. With the right supply chain tools and some knowledge at their disposal, designers can make smart decisions around component obsolescence and remove obsolete components when needed.
Should You Use Obsolete Electronic Components?
The average number of components reaching obsolescence has increased over time. There are multiple reasons for this, including more advanced manufacturing capabilities, greater feature integration (for ICs), and pressure to adapt to quickly changing consumer tastes. There are situations where it is acceptable to use electronic components in a new design. In some cases, such as for maintenance purposes, you might intentionally want to procure obsolete components. Products with long lifecycles demand current components, which requires researching component lifecycle status before beginning a new design. Anytime obsolete components are present in a design, the design team needs to consider the situation and risk involved.
Large vs. Small Original Equipment Manufacturers
Large OEMs, small OEMs, PCB service bureaus, and individual designers can all take different views of obsolescence and sourcing. Larger Original Equipment Manufacturers (OEMs) generally produce at high volume, sometimes reaching millions of units over repeated production runs. Their products need to ideally have the longest possible lifecycle and may need to be procured in huge volumes over a long time period. Obsolete components that are included in a design are not always available in such high volumes and they may reduce the lifecycle of the product. Therefore, it’s critical for OEMs to identify and remove obsolete components when obsolescence affects their ability to continue manufacturing critical products.
Smaller OEMs or design firms using Electronics Manufacturing Services (EMSs) might not be as impacted by obsolete components if they are only producing at low volume and over a short time period. If you choose to include an obsolete component in your design, your EMS will happily place it during assembly as long as you can get the component sent to their facility. If there will never be another board spin, then including an obsolete component may not matter for your design’s quality and functionality.
Obsolete Components Can Be Used for Low-Volume Projects
Obsolete components can be used if a design is only going to be produced at low volume and the obsolete component works well for the design. For example, if you are only going to produce less than 100 printed circuit boards, and there are thousands of units of your obsolete component on the market, including it in the design may not impact the product. However, if the product needs to be produced again later, there is a risk the product needs to be redesigned around newer components.
Avoid Obsolete Components for Larger Projects
Using obsolete components for long-term or high-volume projects can create an unacceptable risk of redesign. During successive manufacturing runs, a board may need a redesign to remove obsolete components. This is particularly important in projects using highly specific or specialized parts for which a replacement is difficult or impossible to find. In some cases, finding an identical replacement component, or as close a match as possible, will suffice.
Failing to plan for obsolete electronic components internally may force designers to rush out new designs without proper testing. If a distributor stops producing a required component, a manufacturer may also need to forge new relationships with other distributors, change authorized distribution channels, or decide whether existing components can be repurposed. This takes time and effort a manufacturer may not have, thanks to tight schedules, client demands, and import/export regulations for some products.
It is also important to note that some obsolete electronic components contain hazardous materials, which could force a manufacturer to rethink their use of obsolete components. If you want to comply with regulations on lead, you’ll need to use components that are marked “Pb-free”. Note that some components may be RoHS compliant but can still contain hazardous substances like lead.
How Should Designers Handle Obsolete Electronic Components?
Planning and communication are essential for handling component obsolescence. Even with the best planning possible, an End Of Life (EOL) notice from a manufacturer can cause significant problems for an industry. No single approach works well for every industry or company, and planning for obsolete electronic components is a dynamic process.
Develop a Strategy to Source Hard-to-Find Components
Usually, after a manufacturer releases an EOL notice, companies using the obsolete component can still get the component through other distributors for a time. Companies should have a strategy for sourcing hard-to-find components, preferably through a reliable source. The more obsolete electronic components a company uses, the more complex the sourcing strategy is likely to become. Companies should not assume a single distributor can meet all of their needs for electronic components. Swapping obsolete components with replacements is just one aspect of periodically redesigning products to keep extending their lifetime.
The process of searching for distributors should ideally happen before a component becomes obsolete, but that isn’t always possible. Companies may need to scour unconventional sources, such as forums or community web sites. The risk of counterfeit parts or disreputable distributors increases with these sources, so companies should exercise caution when using them. Fortunately, there are also reputable sources of obsolete parts, including specific subsets like changeparts or OEM parts.
How Can Designers Avoid Obsolescence Problems?
Perhaps the best way to avoid early component obsolescence is to maximize the lifespan of electronic components. This doesn’t mean constant repairs or overuse to the point of the components no longer functioning at top performance. It means making smart component choices with an eye on where the component is located on its lifecycle curve, an example of which is shown below.
Research the Lifespan of Your Components
The average lifespan of an electronic component has diminished over the years. Selecting a component with a known lifespan shorter than that of its project sets the project up for problems with obsolescence. If possible, designers should make sure a component will be available throughout the predicted lifespan of their project. These predictions are called strategic parts forecasting, and should rely on as much data as possible.
Continuously Analyze Data and Stay Up-to-Date on Industry Trends
Exercising tight control over the supply chain gives a manufacturer up-to-date information about all components in a project and helps avoid unexpected obsolescence problems. A working project could find its way into the hands of consumers when more than half of its components are already obsolete, and a manufacturer could be unaware of this. Periodic audits of a project’s Bill Of Materials (BOM) could warn manufacturers of impending problems and avoid costly redesigns. A type of risk analysis called Materials Risk Index (MRI) could also prevent new designs from using obsolete electronic components. Continued data analysis and knowledge of trends in relevant industries can save projects from commercial or financial failure due to obsolescence.
Ultra Librarian gives designers tools to easily cross-reference data, helping them identify obsolete electronic components. Working with Ultra Librarian takes the guesswork out of preparing for your next great device and puts your ideas on the road to success. Register today for free.