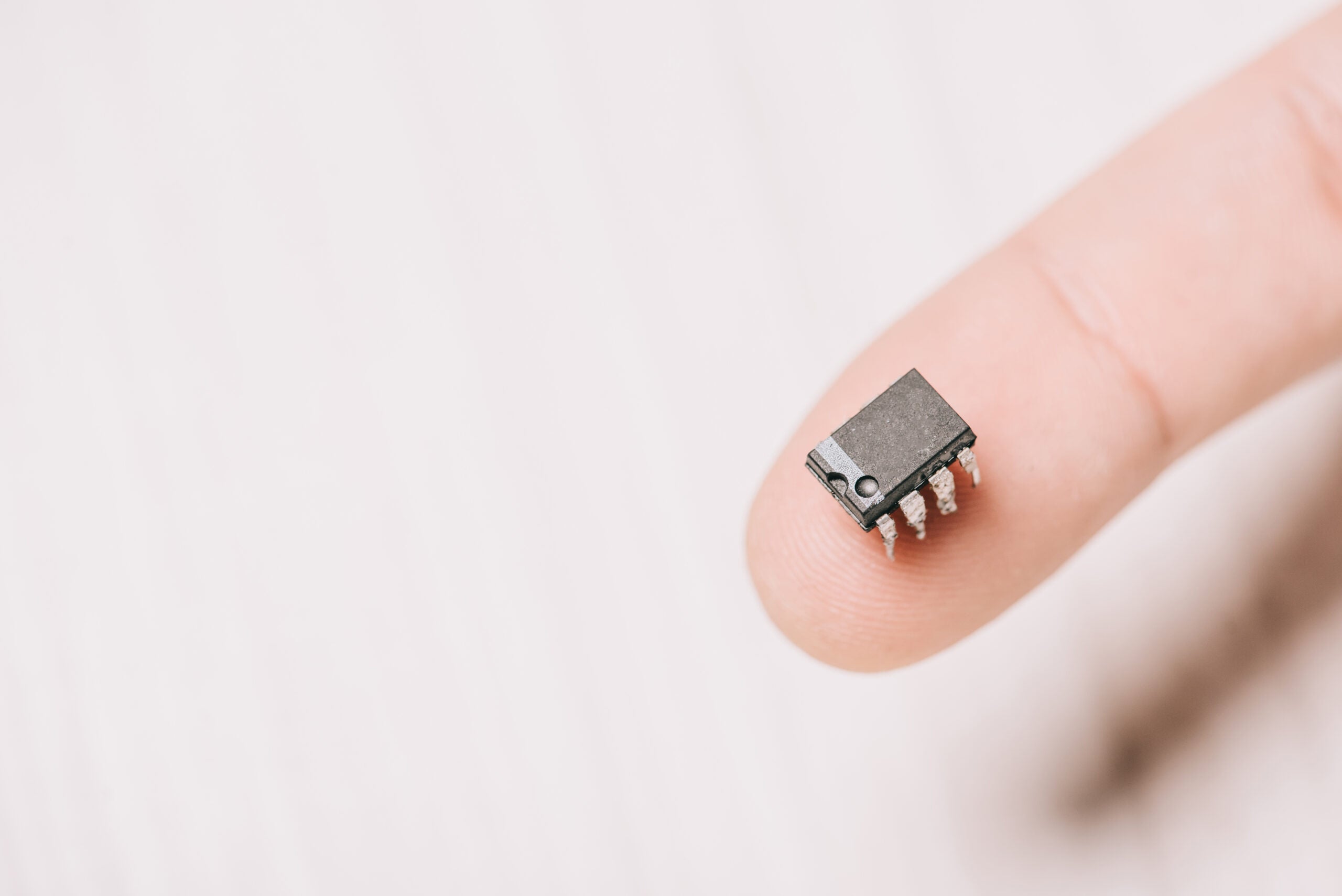
Electronic components inventory management is necessary to balance project resource needs and costs. Without accurate inventory management, it’s easy for manufacturers to over- or under-procure the stock for production, potentially endangering project budget or deadlines. Overseeing electronic component inventory management can be challenging, but a few tried-and-true methods help reduce the legwork involved.
The Various Aspects of Electronic Component Inventory Management |
||
Simulation |
The first step to building an electronics project is to simulate the design to determine the functional characteristics. While there’s no physical inventory management at this stage, the fluid nature of the design can lead to multiple prototype developments. |
|
Sourcing |
There are many component vendors available, but finding the best combination of price, bulk availability, and lead times will require a concerted effort. Components in short supply may require separate fulfillments. |
|
Procurement |
After acquiring the components, contract manufacturers (CMs) need some level of organization to prepare for assembly. Approaches include kitting or searchable trays for larger components. |
|
Assembly |
Depending on package types, manufacturers may use wave soldering, reflow soldering, manual soldering, or a combination. Generally, fewer soldering processes are more cost effective and generate less thermal wear. |
Electronic Component Inventory Management Considerations
Electronic component inventory management can be challenging due to the divide between ordering/purchasing and accounting for physical stock on hand. Keys to consider are listed below.- Bill of Materials (BOM) – The bill of materials is the formal declaration of the schematic – after simulation and mostly finalizing the feature scope of the design, the BOM becomes the component blueprint for the project. Note that the BOM (much like the rest of the project) does allow for some adjustments as the design evolves: things like do-not-install components (DNI) support prototype variance and compensation for test measurements.
- Procurement – One of the foremost challenges of acquiring component stock is forecasting shortages and price shocks to prevent production schedules from running past deadlines or over budget. An assembly shop’s procurement team can analyze market trends and use historical market data to stay ahead of changes to supplier inventory, while anticipating the most efficient purchasing window. Alternatively, the procurement team can seek replacement components with similar electrical performance and packaging to sidestep supply issues.
- Kitting – One process for accurately managing inventory stock is to use a pre-sorting process known as kitting. With kitting, a technician collects all components necessary for a design. While time-intensive on the front end, this method saves significant time during assembly (especially when there are multiple components to hand solder) as it reduces search-and-retrieval time for expansive component storage. However, kitting is less useful for larger operations using automated SMD soldering (i.e., pick-and-place reels) due to the size of the components and the integrated reel packaging.
How to Mitigate Inventory Issues
Pivoting between different components for lean manufacturing practices ensures that a project stays on target (and on budget) regardless of changes in component cost, availability, and lead times. As many designers have witnessed in recent years, supply shocks can rapidly undermine projections. Some suggestions to circumvent component shortages include:- Building on-site stock—Manufacturers may desire to amass common or in-demand components beyond per-project procurement. While the upfront cost is undeniable, projects become much less susceptible to rapid market changes. However, manufacturers do have to account for extra storage space and beware of design obsolescence, which can render components less viable.
- Leveraging vendor relationships – While designers shouldn’t expect a magic bullet for inventory woes from their vendors, building rapport with experienced and trustworthy vendors can mitigate some of the challenges of navigating supply chain issues.
- Sourcing equivalent components – When it becomes too challenging to source a particular manufacturer’s part number (MPN), it is paramount to identify and incorporate components with equivalent electrical functionality. The foremost concern is the packaging: pinouts, layout, size, and soldering techniques may all change between equivalent components, and it’s the responsibility of the design team to ensure the design supports any of these alterations.